AIRBOXER
The Airboxer is a long range unmanned helicopter with a three-blade single rotor. Because of its size, weight and capabilities, it creates a class on its own and brings industrial reliability into the UAV market in an unprecedented small size. High Eye believes its product should be safe to operate under nearly all circumstances and conditions, throughout the year. The Airboxer has been developed over a period of more than 10 years and has been tested under the most extreme conditions on several continents. It has been proven to deliver reliability and capability at any time, wherever it is needed.
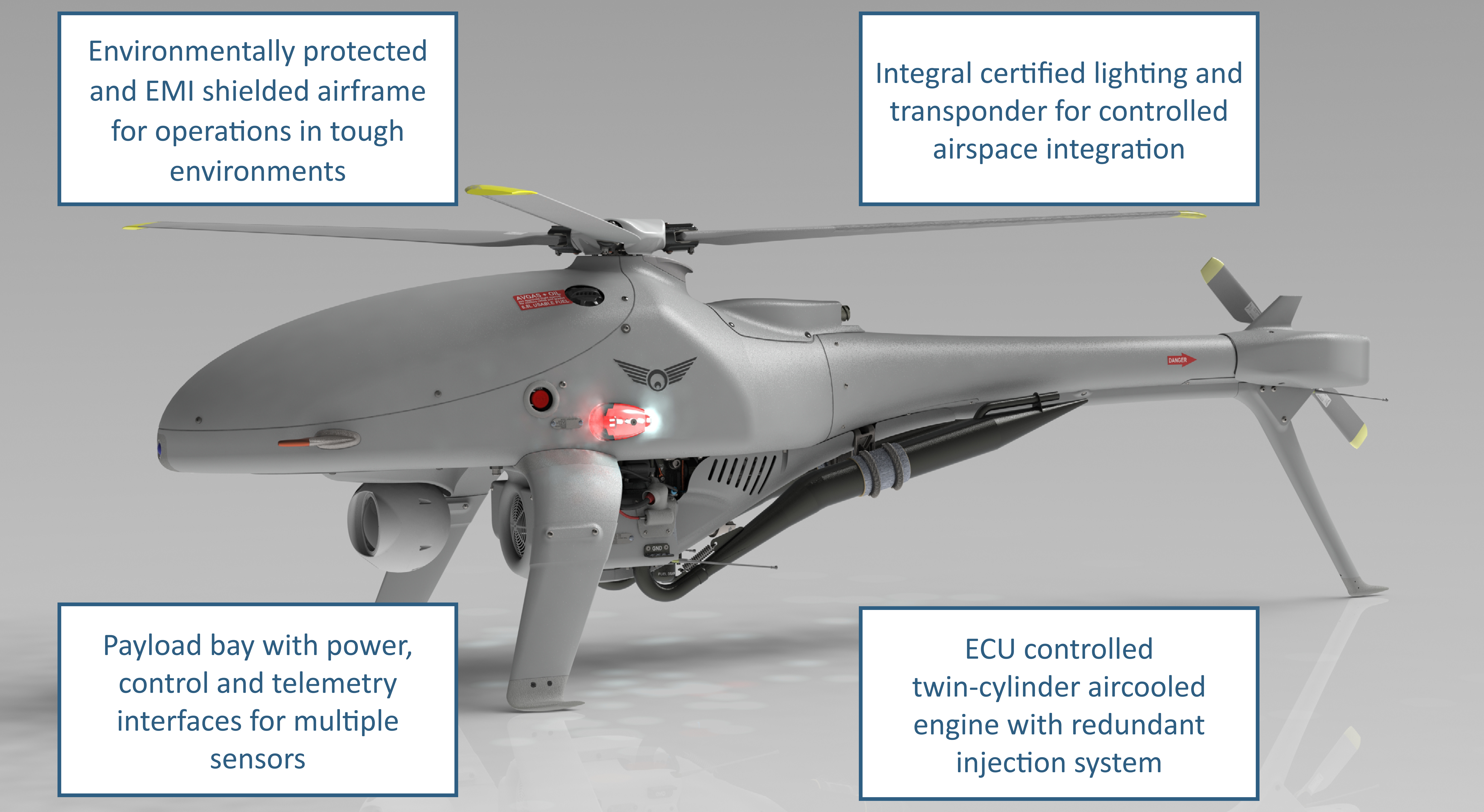
Technical
General Construction
The best way to understand the Airboxer and its capabilities, is by starting to imagine a down-sized version of a manned helicopter. A combination of well-proven aviation technology and modern materials, merged with state-of-the-art electronics, make the Airboxer what it is – an unmanned helicopter platform with global operational capabilities. The technical heart of the Airboxer is centered around the main drive-train, which is surrounded by the rotor systems, fuel system, avionics, sensors and a variety of antennae. The whole helicopter is engulfed by an aerodynamic composite shell, which also serves as the main support structure for all internal systems.
Drive Train and Rotor Systems
High Eye has chosen a classical main- & tailrotor layout for the Airboxer. The rotors have been designed for maintenance-free operation between overhauls, using fully sealed oil-lubricated bearing packs and abbrasion protected composite rotor blades. The main- and tailrotor gearboxes are based on over-dimensioned gear sets and titanium shafts, enclosed and environmentally sealed with permanent lubrication. Both the gearboxes and the rotor systems are rated and tested for a TBO of 1000 hours within standard operational conditions.
Powerplant and Fuel System
Propulsion is provided by an air-cooled boxer engine with fuel injection. Since operations at high altitudes and temperatures have been in mind from the start, the powerplant has a very high power rating for this size of airframe. The operation of the engine is monitored and controlled by a sophisticated ECU, which works in close harmony with the autopilot. The forced air-cooling allows continuous operations in hot & high conditions without negatively affecting the powerplant’s service life. The engine’s injection system is supplied with fuel by a maintenance free, redundant fuel pump module. The aircraft’s main fuel tank has a 8.85 liters fuel capacity.
Electronics and Avionics
All vital electronics on board the Airboxer are enclosed in a central module, located in the forward bay of the fuselage. The module protects the avionics from the outside world, including a high level vibration protection, MIL spec compliant EMI shielding and a dust- and waterresistant rating of IP-67. The very core of this module is formed by the autopilot, which is based on redundant CPUs and IMUs, cooperating with a third external IMU and a whole range of additional sensors. The module also contains the primary and secondary communications radios, the engine’s ECU, a back-up battery system and the alternator’s power convertor. The Airboxer’s alternator is mounted integrally in the main gearbox and powers all electronics and payload systems.
Sensors and Antennae
Although any UAV is full of sensors, High Eye has strived to keep this to an essential minimum. Sensory points of failure have either been reduced to the lowest possible level, or have been protected by a level of full redundancy. External sensors have been protected against EMI influences through shielding, filtering and software back-ups. The UAV’s flight control systems and communications equipment require a vast array of different antennae, which have been integrated into the airframe, reducing aerodynamic drag and improving the airframe’s ruggedness for transportation. Two in-house developed pitot tubes provide barometric inputs to the avionics and are electrically heated for in-flight icing protection.
Corrosion Protection
Having had maritime operations in mind from the start, High Eye has taken corrosion protection to a class-leading level. Drive train components consist mainly of aircraft-grade titanium and surface treated aluminium. Sensitive components are environmentally sealed, whilst all fasteners are designed to reduce chances of contact erosion. The rest of the airframe mainly consists of composites and resiliant plastics. External electrical connectors and interfaces meet IP-67 requirements and tolerate saline conditions. External bearings and hinge points are largely based on industrial polymer bearings, allowing maintenance free operations in the toughest conditions.
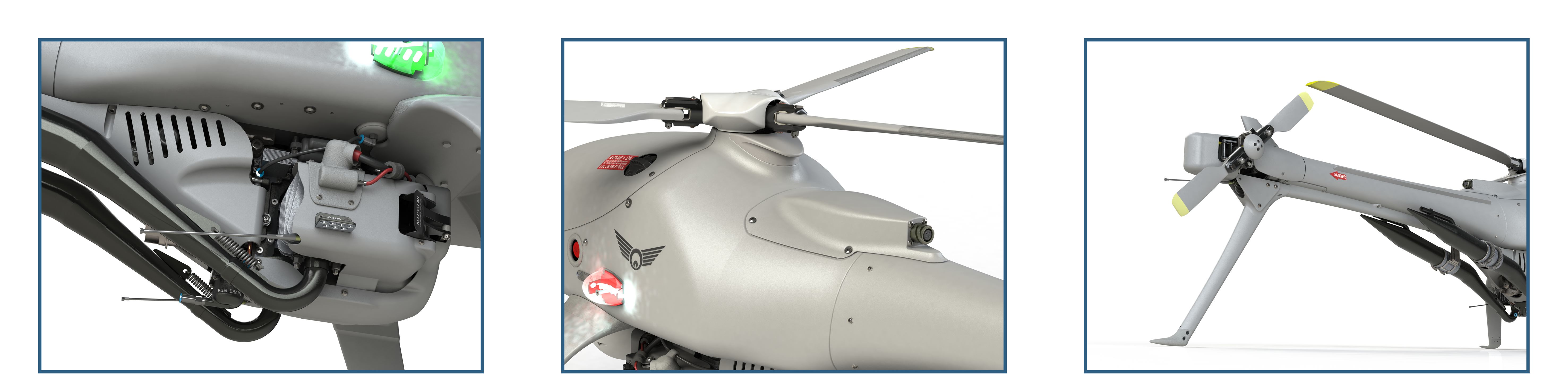
Performance
Multi-Mission Capability
The combination of combustion engine technology, military grade communications equipment and clever design, make the Airboxer a real performer. It will come to its right within the widest variety of missions, be it long-range night-ops from a tactical vessel, to elaborate wild-life research mission in arctic regions. Its strength lies in the combination of long-endurance multi-sensor capability and the capability to operate basically from any area in the world – without additional hardware.
Endurance, Weight and Altitude
Taking ISA sea level conditions as the frame of reference, the Airboxer will lift payloads of 7.0 kilograms for several hours, at sea level. In the same environmental circumstances, it will be able to fly in excess of three hours at a speed of 30 knots with a payload of 5.0 kilograms, or accelerate onwards all the way up to 70 knots. The maximum take-off weight of the aircraft at sea level is 32.0 kilograms and is gradually reduced up to the rated service ceiling, at a density altitude of 10,000 feet.
Fuel Range and Radio Range
Any helicopter will see an improvement in fuel economy at a certain speed, the Airboxer will achieve its maximum range and endurance at a speed of 30 knots. At this speed it will be able to cover in excess of 180 kilometers on one fuel tank with a medium payload capacity. The primary communications data-link provides bandwidths in excess of 45 Mbit/s, and will still be able to achieve 10 Mbit/s at a clear line-of-sight range of more than 50 kilometers, retaining full high-definition video transmission capability.
Environmental Capabilities
The Airboxer’s flight control design and powerplant configuration allow the helicopter to be operated in a wide variety of environmental conditions. Standard operations are allowed in temperatures down to -20 degrees Celcius, up to 45 degrees Celcius and at a humidity of 95%. The UAV tolerates winds up to 25 knots for take-off and landing and moderate levels of rain, snow and hail. Electro magnetic interference has been demonstrated to pose no risk to the Airboxer at frequencies of 1 MHz to 18 GHz and field strengths of 200 V/m. When operating from a ship, roll and pitch angles of the deck are allowed up to 8 degrees and sea state 5 in standard operations.
Autonomy and Flight Modes
To adapt the system to ever-changing mission requirements, a variety of flight modes can be used to operate the Airboxer. All flight modes can be activated or changed at any time during flight. The autopilot provides both semi- and fully automatic flight modes, including multi waypoint following capability, automatic take-offs and landings and clearly defined back-up modes. The Airboxer can also automatically take-off and land on a moving ship, or follow a ship in a configurable orientation as it sails or changes course. In the event of a full loss of the redundant communication, the UAV is capable of following pre-determined routes, waypoints and altitudes, to bring it to an area which has been designated for the following automatic landing. Automatic navigation is made possible through a combination of barometric, magnetic and GPS based external inputs, and can be sustained at high accuracy when an input is lost. Multiple sensory failure leads to pre-defined flight modes which allow safe retrieval of the helicopter.
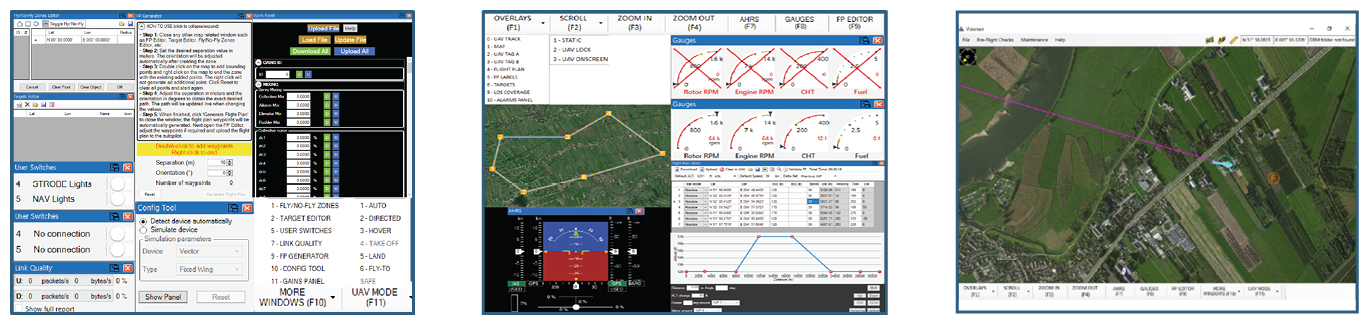
Payload
Flexibility by Design
Multiple payloads, sensors and other additional hardware can be integrated with ease on the Airboxer, to expand its capabilities and to fulfill a dedicated mission. Whilst some equipment is available as standard options, others can be integrated on request. The Airboxer is generously equipped for mounting odd-sized hardware to the airframe and to provide communication and electrical power for any UAV payload system within a certain weight range. Generally, payloads can be integrated with a total integrated equipment weight of up to 7.0 kilograms. A variety of different voltages and current ratings are supplied by the UAV’s electrical system to the payload. Depending on the final configuration and mission profile, payload communication data rates in excess of 30 Mbit/s can be handled by the Airboxer’s communication system.
Payload Integration
In the ever expanding market of UAV payloads, High Eye has chosen payload integration flexibility over offering a range of fixed payloads. Customers are free to select any third-party payload, as long as it fits the Airboxer’s payload capabilities. Over the years, High Eye has integrated different size stabilized payloads, with electro-optical, infrared and laser based sensors. A lot of experience has been built up to find the optimum in vibration-isolation without affecting the required high accuracy. Other integrated equipment includes LiDAR, synthetic apperture radars, survey-magnetometers and gas detection equipment.
Airspace Integration
To aid integration on airfields and into controlled airspace, the Airboxer can be expanded with several compliant or certified aeronautical options. The MXS line of ADS-B In & Out transponders has been fully integrated into the UAV’s software. When the Airboxer is equipped as such, the transponder can be controlled through the GCS and transmit up to mode S. Standard options also include a full complement of FAR23 compliant aircraft lighting, including navigation/position lights, strobe lights and a beacon/anti-collision light. All lights can be controlled individually from the GCS during flight.
Maritime Operations
In the unlikely event of an emergency water landing, an automatically inflating flotation kit can provide much-needed flotation capability for the Airboxer. The optional automatic flotation bag inflates when beeing submerged and provides a highly visible reflective bag, to aid finding and recovery of the UAV from the water surface. For airline transport and long-term storage, the system can be de-armed. Other maritime payload equipment can include fully integrated AIS receivers or EPIRBs.